Plating & Coatings
Plating neodymium magnets is an important process to protect the magnet against corrosion. The substrate NdFeB(Neodymium, Iron, Boron) will oxidize quickly without a protective layer. Below is a list of platings and their effectiveness in certian environments.
All of the Neodymium Iron Boron we stock are protected. The majority are Ni-Cu-Ni plated which consists of 3 layers (Nickel, Copper, and Nickel).
Note: All coatings / platings must be done at the factory before the magnet is saturated(charged). The magnetic field will disrupt the electroplating process, while the heat required for other types of platings would demagnetize the magnet.
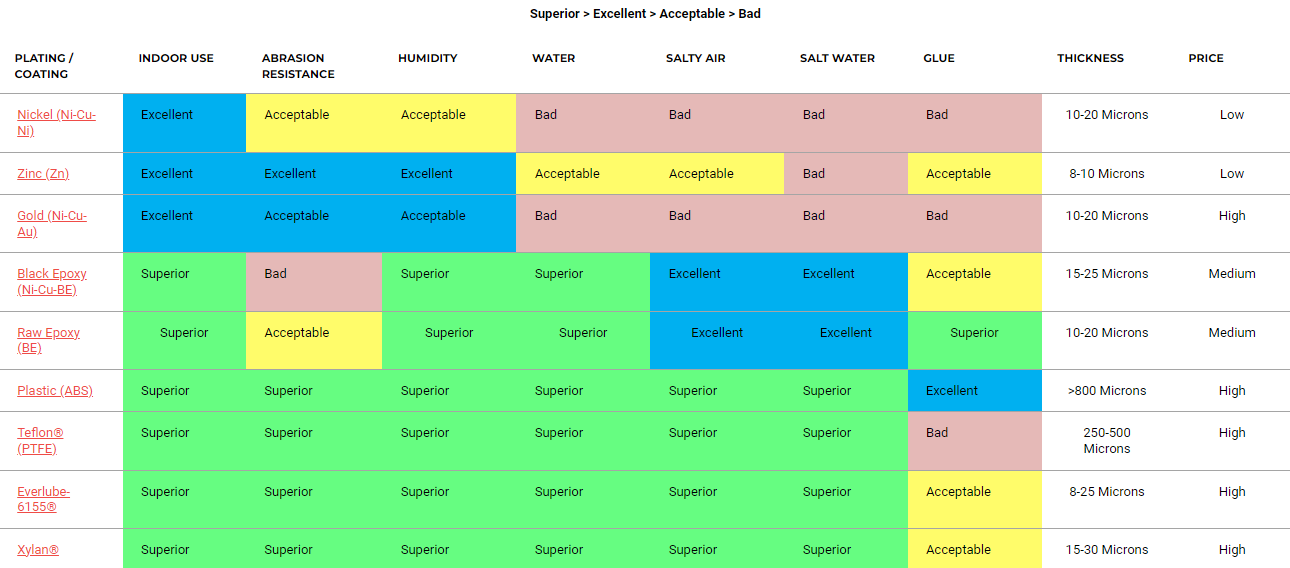
Nickel (Ni-Cu-Ni)
The most common plating. Ni-Cu-Ni is a durable 3 layer (nickel, copper, nickel coating). Great for indoor use. They may be used outdoors if protected from rain and humidity.
Good abrasion resistance.
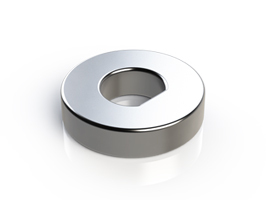
Zinc (Zn)
Zinc is a standalone (one layer) plating. Zinc is self-sacrificing, meaning when it starts to oxidize the outside turns white creating a durable layer of protection.
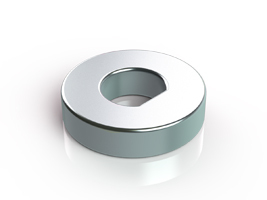
Gold (Ni-Cu-Ni-Au)
A very thin/cosmetic layer of gold. Usually produced with an underlying layer of nickel to create a brighter finish.

Black Epoxy (Ni-Cu-BE)
Black Epoxy plating consists of 3 layers Nickel, Copper, and Epoxy exposed as the top layer. Great for outdoor applications. However, black epoxy is not as abrasion-resistant as other platings. In harsh conditions, the epoxy layer may be scratched off to expose the copper layer underneath.

Raw Epoxy (BE)
Raw Epoxy is designed specifically for gluing applications where the magnet requires a good adhesion to epoxy glue.
This coating consists of one layer of epoxy covering the magnet.

Plastic (ABS)
ABS Plastic is highly corrosion resistant. This coating requires an injection mold to be created in order to encase the magnet. The plastic shell needs to be thicker than other coatings so the plastic can flow during the injection process.
Multiple colors available.

Teflon® (PTFE)
Teflon is very resilient and can withstand harsh environments. It is highly corrosion-resistant. An injection mold is required to create the shell around the magnet.
There will be a noticeable mold seam around the magnet where the injection mold separates.

Everlube® 6155
Everlube 6155 Is An Aluminized Barrier Coating Specially Formulated To Maximize Adhesion And Corrosion Protection When Applied To Rare Earth Magnets.
The Coating Is Very Durable And Provides Excellent Chemical And Corrosion Resistance.

Xylan®
Xylan coatings are fluorocarbon coatings that contain dry lubricants. Slippery and highly corrosion resistant.
Multiple colors available.
